Plant Process Data Management System (PDM)
Introducing the Plant Process Data Management System: a cutting-edge solution that unifies digital assets into a seamless platform, transforming data into actionable insights. By providing real-time analytics and interactive dashboards, it empowers plant personnel to collaborate effectively, make swift decisions, and drive operational excellence.
Ramco PDM: Eliminate Data Hunting, Enhance Visualization, and
Drive Proactive Decision-Making
Ramco's Plant Process Data Management System (PDM) serves as a
critical middle layer that bridges IT and OT systems, enabling
seamless real-time data flow from the shop floor to the
boardroom. In the complex environment of cement manufacturing,
where multiple production lines and geographically dispersed
plants are common, PDM offers a robust solution to unify and
optimize operations.
Cement plants invest heavily in digital assets like DCS systems,
burner management systems, expert optimization systems,
temperature scanners, laboratory information management systems
(LIMS), and more. These systems, while efficient in isolation,
often create data silos that hinder comprehensive analysis and
decision-making. Traditional methods of manually collating data
from these disparate sources using spreadsheets are not only
time-consuming but also prone to errors, leading to
inefficiencies and disagreements during critical meetings.
PDM eliminates these challenges by integrating powerful
communication drivers capable of concurrently fetching real-time
data from various digital islands within the plant. Advanced
algorithms sanitize and process this data for both real-time and
historical analysis, ensuring that all stakeholders—from
management to production, quality, and maintenance teams—have
access to accurate, up-to-date information.
The system’s visualization and analytics tools deliver intuitive
dashboards and MIS reports, accessible across the plant’s
network on various devices, including workstations, tablets, and
smartphones. By automating data collection and reporting, PDM
saves valuable time, transforms production meetings into
focused, data-driven discussions, and fosters cross-functional
collaboration. This ultimately enhances organizational agility,
improves personnel productivity, and drives operational
excellence across the enterprise.
With Ramco’s PDM, cement plants can transition from reactive to
proactive decision-making, ensuring that every operational
aspect is aligned towards achieving the highest standards of
performance and efficiency.
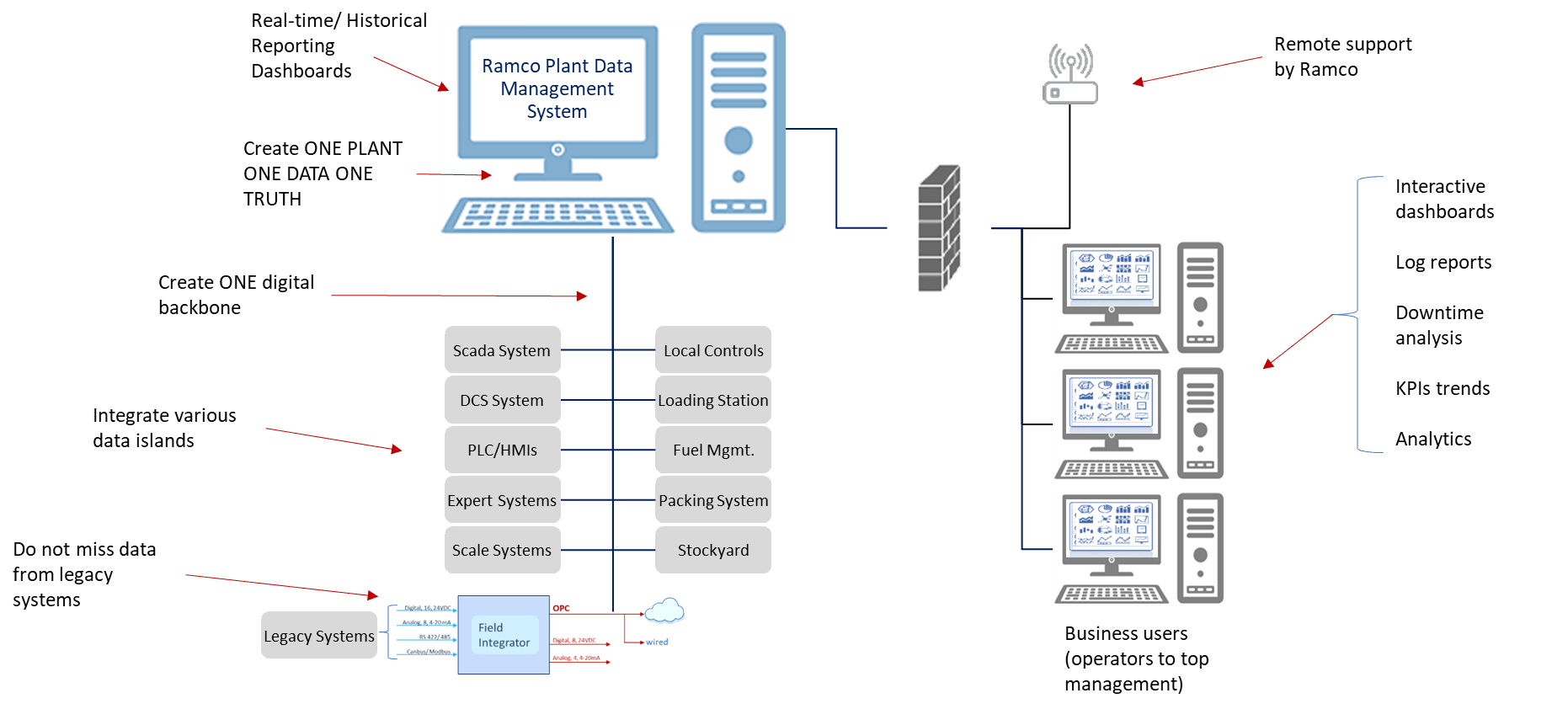
Ramco PDM: The Ultimate Solution for Real-Time Decision Support and Knowledge Management in Plant Operations
Ramco's Plant Process Data Management System (PDM) stands as the
most advanced, versatile, and powerful real-time decision
support and knowledge management system for collaborative plant
operations management. Designed for scalability, Ramco PDM
seamlessly adapts from a single unit—such as a grinding unit—to
a full integrated line, covering everything from limestone
quarrying to cement dispatch, and even multiple production lines
within a single location.
Guided by the "one plant-one data-one truth" principle, Ramco
PDM delivers customizable, interactive dashboards that cater to
the specific needs of plant personnel. Whether you’re a plant
operator, function supervisor, function manager, or plant
director, role-specific, access-controlled dashboards ensure
that your focus remains on the key operational performance
metrics that matter most to your role. These metrics include,
but are not limited to, MTBF, OEE, specific power and fuel
consumption, turnaround time, and stoppage time.
Ramco PDM is not just about data; it's about the stories behind
the data that drive actionable insights. Its powerful analytical
tools enable users to delve into historical data, uncovering
valuable insights that lead to performance improvements. Whether
you're analyzing equipment efficiency, energy consumption, or
process stability, PDM empowers you to take informed actions
that enhance overall plant performance.
Built-in Statistical Process Control (SPC) algorithms go beyond
merely displaying trend curves; they interpret the underlying
reasons behind those trends, providing you with the critical
insights needed to understand why a process parameter is
behaving a certain way. This deep level of analysis transforms
raw data into meaningful narratives, helping you to anticipate
issues, optimize operations, and ultimately drive continuous
improvement across your plant operations.