TargetSuite
In complex industrial environments, where equipment dynamics, process conditions, and raw material characteristics vary continuously, maintaining optimal performance requires intelligent, adaptive control strategies. TargetSuite is an advanced Machine Learning (ML) layer built over ProcessSuite’s Model Predictive Control (MPC) framework, designed to enhance real-time decision-making by dynamically adjusting process targets. By leveraging data-driven optimization models and AI-powered target recommendations, TargetSuite continuously evaluates plant conditions, detects deviations, and recalibrates controller setpoints to sustain peak efficiency, product quality, and energy minimization—critical global KPIs. Its self-learning algorithms identify the most efficient operating regions, ensuring controllers proactively adapt to evolving process constraints. This real-time optimization capability reduces reliance on human intervention, enabling adaptive process autonomy and pushing the plant toward self-optimizing, autonomous operations. By seamlessly integrating with existing APC frameworks, TargetSuite enhances process stability, throughput, and energy efficiency, all while minimizing operator workload. With TargetSuite, AI-driven intelligence transforms industrial optimization—delivering smarter, more resilient, and autonomous plant operations.
Key Benefits
- Self-learning AI models continuously improve target recommendations.
- Dynamic adaptation ensures sustained process efficiency and stability.
- Seamless APC integration enhances existing control systems.
- Reduced operator dependence, pushing the plant toward autonomous optimization.
- TestSuite Technology
- TargetSuite - User Interface
TargetSuite RTO: AI-Driven Target Adaptation for Dynamic Process Optimization
TargetSuite RTO employs advanced Machine Learning (ML) and AI-driven analytics to enable real-time target adaptation for process industries. The system ensures controllers continuously adjust to changing process dynamics, optimizing primary and secondary variables to sustain peak performance.
Inference Variables Acquisition
Collects critical process parameters, raw material properties, and product quality indicators across an extended historical window (e.g., 6 months). Focuses on key operational factors such as burning zone indicators in cement manufacturing.
Data Preprocessing & Normalization
Applies data filtering, noise reduction, and normalization techniques to enhance data integrity and remove anomalies. Ensures that variations in input parameters are standardized for high-precision model training.
Dimensionality Reduction & Feature Extraction
Utilizes advanced dimensionality reduction algorithms to eliminate redundant variables and improve computational efficiency. Extracts high-impact process features, enabling data-driven insights into system behavior.
Machine Learning-Based Optimization
Employs AI/ML models, including supervised and unsupervised learning, to determine the best operating region dynamically. Learns from historical and real-time data to predict optimal setpoints and process targets.
Real-Time Target Adaptation
Dynamically adjusts primary and secondary process control targets to bridge the gap between current and optimal operating regions.
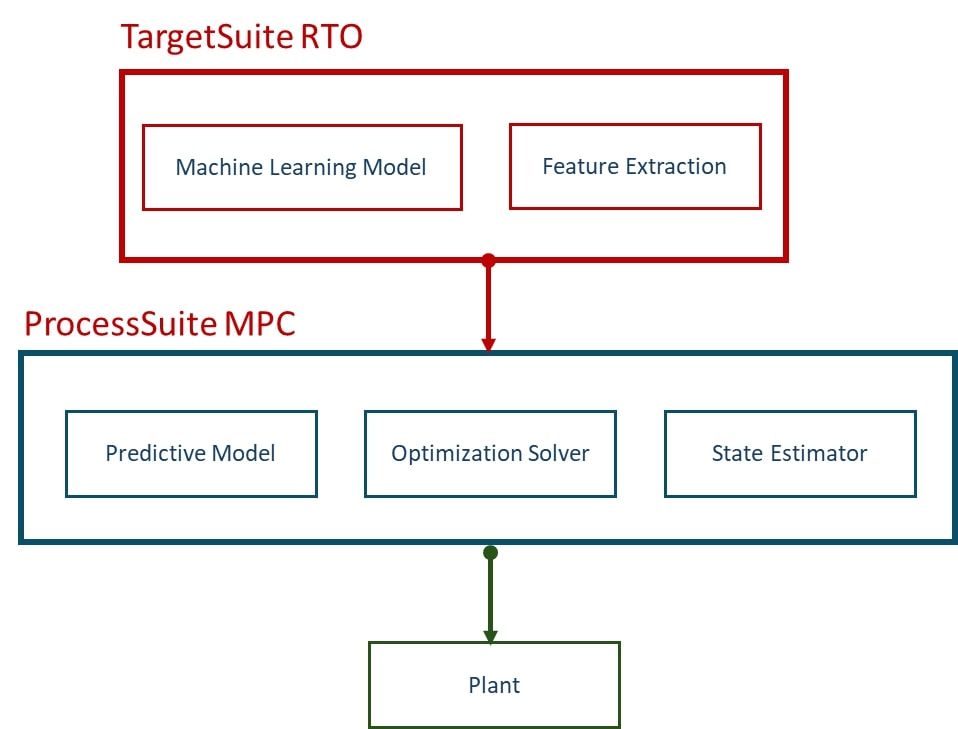